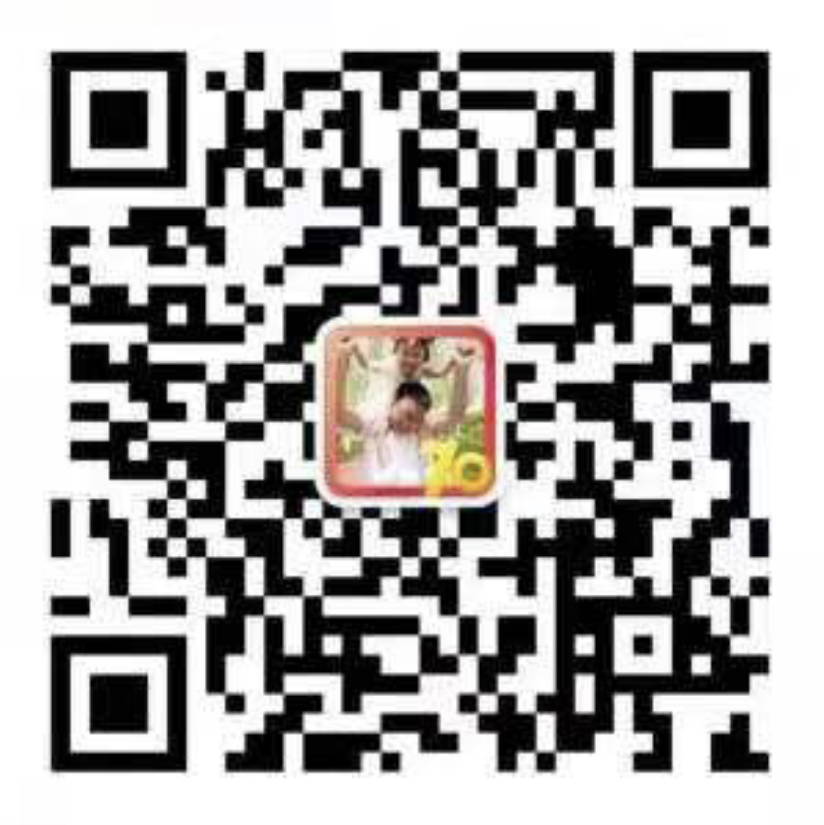
本文對(duì)鑄件兩種不同位置的夾砂缺陷的產(chǎn)生原因進(jìn)行了分析,并結(jié)合生產(chǎn)實(shí)際從型砂性能、鑄件結(jié)構(gòu)與澆注系統(tǒng)等方面提出改善措施,使不同位置的夾砂缺陷均得到解決。
一、夾砂缺陷原因分析
夾砂缺陷是鑄件生產(chǎn)中常見的一種表面缺陷多產(chǎn)生于潮模砂鑄造時(shí)鑄件較大的表面。通過對(duì)夾砂缺陷進(jìn)行統(tǒng)計(jì),夾砂的廢品率高達(dá) 1.90%嚴(yán)重影響了鑄件質(zhì)量。氣缸體鑄件夾砂缺陷主要有兩大類,一類是出現(xiàn)在下箱的位置,第二類出現(xiàn)在上箱處的位置。
對(duì)于下箱位置處的夾砂缺陷,主要由于澆注系統(tǒng)中內(nèi)澆道口直接對(duì)準(zhǔn)產(chǎn)生夾砂的砂胎位置,造成夾砂部位在高溫金屬液的沖刷、擾動(dòng)、沸騰熱作用下,砂型表面急劇受熱,形成高濕度、低強(qiáng)度的凝聚層叫,由于型砂的強(qiáng)度不能阻止膨脹砂層的橫向滑移,砂層表面發(fā)生分層和破裂,金屬液就有可能鉆入砂層形成夾砂。
對(duì)于上箱位置的夾砂缺陷,其產(chǎn)生的主要原因是由于澆注高溫液態(tài)金屬時(shí),砂型的表面層受鐵水輻射傳熱,體積膨脹產(chǎn)生熱應(yīng)力。在熱應(yīng)力的作用下,最可能的破壞方式是失穩(wěn),所以夾砂的力學(xué)實(shí)質(zhì)是薄板的受壓失穩(wěn),其產(chǎn)生過程是鑄型上表面受熱膨脹,受到周圍鑄型阻礙,內(nèi)部產(chǎn)生熱應(yīng)力,當(dāng)應(yīng)力超過某一臨界值時(shí),砂型表面失去水分形成干燥層,失穩(wěn)而彎曲,尺寸增大,干燥層宏觀膨脹量越大,失穩(wěn)拱起也就越大,在撓度大于水分飽和區(qū)可能產(chǎn)生的伸長量的區(qū)域,干燥層與水分凝聚區(qū)分離,熱應(yīng)力大于抗拉強(qiáng)度時(shí)產(chǎn)生裂紋,干燥層斷開,產(chǎn)生夾砂。
二、砂缺陷解決措施
2.1 提高型砂熱濕拉強(qiáng)度及增大型砂退讓性由于夾砂缺陷實(shí)際上是由于砂型與鐵水直接接觸使其表層的型砂失去水分,形成干燥層,干燥層受壓失穩(wěn)而產(chǎn)生,若垂直于干燥層方向的熱濕拉應(yīng)力(由水飽和凝聚區(qū)產(chǎn)生)作用于干燥層的剛性差的方向,則很小的熱濕拉應(yīng)力就能產(chǎn)生較大的抵抗失穩(wěn)的彎矩,增大熱濕拉強(qiáng)度可以減少鑄件的夾砂缺陷3,因此采用熱濕拉強(qiáng)度較高的優(yōu)質(zhì)鈉基膨潤土有利于降低夾砂缺陷。在型砂中當(dāng)煤粉的質(zhì)量分?jǐn)?shù)由0.4%逐步降低到0.1%時(shí),鑄件的砂缺陷明顯增多,這說明降低型砂退讓性,夾砂缺陷將明顯增加。為此進(jìn)一步優(yōu)化砂處理工藝以降低鑄件的夾砂缺陷:
1)在每次生產(chǎn)時(shí),6000kg砂型中比原來增加3kg膨潤土,同時(shí)保證緊實(shí)率在36%以上;
2)在制的型砂中發(fā)現(xiàn)有小砂塊及混不的現(xiàn)象,為減少混砂機(jī)圓盤出來大塊型砂,延后了粉塵加人時(shí)間,將18s改為28 s;延長了二次加水前的混砂時(shí)間,將69s改為 77s;延長了二次加水后的混砂時(shí)間,將133s為144s;
3)增加舊砂的排除,新砂的加入,避免死灰含量過高及化現(xiàn)象加重造成的型砂變脆;
4)增加煤粉的添加量,不僅可以提高型砂的退讓性,分散減少型砂膨脹時(shí)的力,同時(shí)煤粉受熱時(shí)的焦化性提高了型砂表層的抗拉強(qiáng)度。通過以上砂處理優(yōu)化,型砂熱濕拉強(qiáng)度及退讓性均有了較大改善。2.2 增加應(yīng)力釋放槽及防夾砂釘當(dāng)濕型鑄造的鑄件為大平面,型砂膨脹率大濕強(qiáng)度低,水份過多,透氣性差,鑄型排氣不良,鑄件的高水層強(qiáng)度低,以及由于鑄型表面干燥層膨脹而與鑄型本體分離開來,能自由地滑動(dòng),而且臨界應(yīng)力與鑄型頂面尺寸的平方成反比,臨界壓應(yīng)力將隨鑄件尺寸的增大而急劇減小,所以具有大平板結(jié)構(gòu)的鑄件特別容易產(chǎn)生夾砂,同時(shí)尺寸越大,更大撓度越大,分層區(qū)域越大,鑄件易產(chǎn)生夾砂缺陷,因此解決大平面夾砂問題就需要破壞大平面。通常在容易產(chǎn)生夾砂的大平面劃出應(yīng)力釋放筋或增加防夾砂釘。
應(yīng)力釋放筋的尺寸,會(huì)影響夾砂的預(yù)防效果干燥層的厚度一般為5mm~7mm,而應(yīng)力釋放筋的厚度應(yīng)該超過干燥層,釋放筋的寬度應(yīng)盡量小P。為此在下型夾砂位置增加寬度為5mm深度為8mm的筋,造型時(shí)在型砂表面形成網(wǎng)格切槽,分割了平面,增加型砂的退讓空間,同時(shí)還可以加強(qiáng)鑄型,減少夾砂缺陷的傾向。
對(duì)于上型位置的夾砂缺陷,采取了增加直徑為6mm防夾砂釘,同樣可以破壞夾砂平面,此種方法對(duì)于解決夾砂缺陷效果明顯。
2.3 優(yōu)化澆注系統(tǒng)
澆注工藝是否合理對(duì)鑄件產(chǎn)生夾砂類缺陷有很大的影響間。對(duì)于下箱位置的夾砂缺陷,通過對(duì)澆注系統(tǒng)與夾砂位置進(jìn)行對(duì)比,發(fā)現(xiàn)第 5 瓦口的澆道直接對(duì)準(zhǔn)了產(chǎn)生起皮夾砂臍子的砂胎位置,高溫鐵水注人時(shí),對(duì)此處的砂型容易產(chǎn)生沖刷,特別是當(dāng)澆注速度較快時(shí),對(duì)型砂的沖刷作用力更大,使砂型表面急劇受熱發(fā)生水分的遷移和體積膨脹,熱壓應(yīng)力超過水分飽和凝聚區(qū)的熱濕拉強(qiáng)度,砂型表面產(chǎn)生破裂,從而產(chǎn)生夾砂。為此,將5瓦口的靠近夾砂位置內(nèi)澆道去掉,避免鐵液直接對(duì)準(zhǔn)臍子位置的砂胎,減小沖刷。更改后下型此位置的夾砂缺陷消失。
三、結(jié)論
根據(jù)上箱、下箱兩種不同位置處的夾砂缺陷產(chǎn)生原因的分析,采取了相應(yīng)的改進(jìn)措施:
1)對(duì)于上箱位置處的夾砂缺陷,主要通過增加防夾砂釘措施,破壞夾砂位置的大平面,減小熱壓應(yīng)力;
2)對(duì)于下箱位置處的夾砂缺陷,主要是通過優(yōu)化澆注系統(tǒng),避免內(nèi)澆道口直接對(duì)準(zhǔn)產(chǎn)生夾砂的砂胎位置,防止沖蝕夾砂,同時(shí)在夾砂位置增加合適尺寸的應(yīng)力釋放槽,使型砂表面形成網(wǎng)格切槽;
3)對(duì)于以上兩種位置的缺陷我們同時(shí)采取了提高膨潤土、煤粉加入量,降低死灰含量,保證型砂混制的均勻性等工藝措施來提高型砂的熱濕拉強(qiáng)度及型砂的退讓性,從而提高型砂的抗夾砂能力;通過此措施的實(shí)施氣缸體兩種位置的夾砂缺陷已經(jīng)全部消除。
——摘自萬方數(shù)據(jù)